Customized Protective Coatings Meet The Challenge Of Extending Service Life For Rotating Equipment
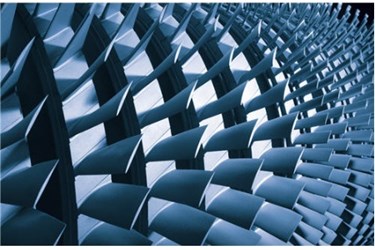
Achieving an acceptable service life without excessive maintenance can be a challenge for rotating equipment that is used in the processing and delivery of hydrocarbon products. Thanks to the latest surface coating technologies however it is possible to offer massive improvements to the expected service life of compressors, turbines and pumps that are subject to surface oxidation, corrosion, erosion and heat damage.
Travis Cockrell, Component Superintendent of the Coating Department at Sulzer’s Houston Service Center, looks at some surface protection processes and technologies that are now being used to increase the durability of rotating equipment used in demanding operating environments.
Long-term reliability is a common goal for all plant operators, achieving it requires a considered approach that takes into account a range of contributory factors and makes use of the most appropriate technology and manpower available to them. Rotating equipment that is in direct contact with the process media and under constant attack, presents a major challenge; it is possible however to reduce degradation to a minimum by selecting the correct coating system.
Generally, turbines, compressors and pumps, are all subject to a variety of environmental conditions that contribute to corrosion, erosion, fouling and various temperature related issues. The first step is to understand the operating environment of the machinery. From there, the sources of degradation can be classified and specific coating systems can be used to increase efficiencies, lengthen the interval between scheduled maintenance and reduce the occurrence of unscheduled maintenance events.
Gas turbines example
The flow path of air and fuel through a gas turbine presents a number of different conditions that can have an adverse effect on the performance of the turbine. The combination of heat, microscopic abrasives and a gradually increasing concentration of corrosive elements can cause significant damage to a once smooth airfoil surface. As the surface finish slowly degrades, the efficiency of both the compressor and turbine is reduced.
Compressor section
This process can be arrested in the compressor section of the gas turbine, and the surface finish restored, by the application of suitable metallic coatings. There is a range of options open to suit the specific duty of the turbine in question, but all include a type of metal deposition where a tough corrosion resistant surface is created.
An aluminum base layer is typically used in gas turbine compressors for corrosion protection of ferritic/martensitic steel components in moist conditions. It provides galvanic protection, which means that small scratches to the surface layer are less likely to cause corrosion. It is produced by spraying a slurry of aluminum and an inorganic binder, rendered insoluble by a medium-temperature baking process. This layer can then be covered by a harder layer that might include metals such as Chromium.
The harder layer is usually applied using a spray coating method such as Chemical Vapor Deposition (CVD), Air Plasma Spraying (APS), Low Pressure Plasma Spraying (LPPS) or High Velocity Oxygen Fuel (HVOF) - which one will depend on the coating thickness required and the sensitivity of the part to heat, as some processes are hotter than others. By applying corrosion inhibiting and surface finish enhancing coatings to the compressor section it is possible to increase the efficiency and extend the service life of the gas turbine.
Hot section
Modern gas turbine hot section components are made using nickel or cobalt based superalloys, which are designed to operate in high temperatures. However, these alloy compositions are less well suited to providing corrosion and oxidation protection and need to be supplemented with custom coatings that can deliver the hot corrosion and oxidation protection required for extended service lives.
The process of oxidation causes a layer of metal-oxide to form on the surface, which, in general, protects the underlying material. Therefore the oxidation process slows down as the thickness of the oxide layer increases. This process can be replicated with the intentional formation of oxides that provide a protective layer preventing further atmospheric attack.
Corrosion of a gas turbine component usually occurs in one of two ways. Hot corrosion may take place between 1450 and 1650 °F and it attacks the entire surface of the component. Alternatively, corrosion at cooler temperatures is more localized and therefore tends to create distinct layers of oxide and exposed metal. Further damage can be caused by erosion which involves repetitive mechanical abrasion by particles in the air stream.
Standalone High Velocity Oxygen Fuel applied MCrAlY coatings are sufficient to combat corrosion/oxidation at lower firing temperature gas turbines. For newer technology, higher firing temperature gas turbines, the combination of a MCrAlY bond coat coupled with a ceramic thermal barrier coating will reduce the surface temperature of the substrate and reduce the degenerative effects of oxidation and corrosion.
Compressors
Pumps and compressors account for more than 20 percent of the world’s electricity demand and the energy costs to run them represent 95 percent of the running costs. It is therefore essential to minimize these costs by improving performance and efficiency; these efforts will also have a beneficial effect of improving reliability and service life.
While turbines extract energy from a gas expansion process, turbofans and compressors are used to increase the energy of gases. As such, the main issues with these components are corrosion, erosion, and fouling.
Corrosion is defined as a chemical reaction between the component surface and the reacting fluid passing through a turbomachine for example. Many metals form oxide layers that adhere to and passivate the surface to prevent further corrosion, but the change in the physical properties of the surface significantly increases the frictional properties and thus decrease aerodynamic efficiencies; so there is a balance to be struck between protection and efficiency, which is where advanced coatings can help.
Particulate fouling results from the presence of small particles in the ingested air streams that can cause a distortion to the oncoming laminar flow. This degrades flow capacity and can reduce the efficiency of the equipment in a short period of time. This is a particularly serious issue in the oil and gas industry where sticky hydrocarbon aerosols are constantly present.
In the harshest of operating conditions, solid and/or liquid particles can pass through the equipment causing erosion. Erosion that results in moderate to severe material loss can change aerodynamic efficiencies significantly. It can also lead to premature blade/vane replacement and failure. In operating conditions where both erosion and corrosion are present, corrosion can be the primary source of attack by weakening the substrate surface. Once corrosion has initiated, the substrate is more easily eroded being the secondary source of degradation.
Modern coating technology can now be applied to legacy equipment that was not designed to take account of particulate-laden gas streams. In this way the original surfaces can be restored and upgraded with greatly improved anti-fouling and corrosion resistance. Implementing a new coating as part of a refurbishment project can significantly improve the performance and reliability of existing equipment.
Coating processes in detail
Oxidation and corrosion resistant coatings - as mentioned previously, are usually aluminides applied by a variety thermal spray or surface deposition techniques. Corrosion resistant coatings will also use an aluminum base coat that is designed to be conductive - allowing for cathodic protection. The aluminum becomes the sacrificial element and therefore protects the less active base metal component. The electrons flow from the aluminum to the base substrate, which becomes negatively polarized and therefore protected against corrosion.
The basic thermal spraying and physical / chemical vapor deposition (PVD and CVD) techniques allow for different coating thicknesses, but also have application restrictions; the spray techniques can be used to apply a thicker layer but need a relatively flat surface and direct line-of-sight in order to accurately apply consistent coating thicknesses. The deposition techniques typically produce a thinner layer but can coat more complex shapes easily.
The thermal spraying process involves heating a material, in powder or wire form, to a molten or semi-molten state. The material is propelled using a stream of gas or compressed air toward the material to be coated, or substrate, creating a new surface structure as it impacts. The coating materials can be melted using several different processes, including HVOF, plasma spray, and electric-arc delivery systems. The process can take place under standard atmospheric conditions or in a special, highly controlled atmosphere.
Applications include protection from wear, high temperatures, or chemical attack, as well as providing a substitute for chromium which can be hazardous in some states. Coatings can be metallic, ceramic or any combination required to meet a broad range of physical criteria.
Anti-fouling
For applications that require improved anti-fouling protection, coatings can be applied to both stationary and rotating blades as well as diaphragms, guide vanes, rotors and impellers. Coatings can be tailored to specific applications and include an aluminum base coat for corrosion protection as well as an inorganic sealer and a specialist non-stick final layer.
These anti-fouling coatings have a thickness between 75 and 125 microns and use polytetrafluoroethylene (PTFE) which gives excellent chemical resistance in low to medium temperatures with a maximum operating temperature of 550 °F. PTFE offers excellent protection from chemical attack from substances with a pH between 3 and 9 as well as resistance to many solvents and fuels. For specific applications that require protection beyond these characteristics, more specialized coatings can be tailor-made to suit a particular application.
Keeping in balance
In all turbomachinery applications, dynamic balance is a crucial requirement, so the application of any coating system has the potential to upset the balance of a turbine or compressor, even if it is only a few microns in thickness. It is therefore essential that the component being coated is checked for balance both before and after the protection layer is applied.
The techniques and equipment used to apply the latest coatings depends largely on the type of coating being applied and the function of the component. Coatings that are designed to provide high temperature corrosion resistance are often applied using a HVOF gun, which produces a dense coating with a high bond strength.
Due to the precision required in manufacturing and maintaining high temperature turbine blades, these coatings should be applied using a robotic manipulator with automated thermal spray equipment. In this way, the coating is applied uniformly on each blade by removing the human error that is associated with hand spraying. Balancing should then be carried out to ensure each machine will operate perfectly after being protected.
Improving efficiency
With such high energy requirements, the hydrocarbon processing industry often uses on-site generation plants and the growing demand for power has led to significant research into improving production efficiency. Essentially this can be divided into combustion efficiency and mechanical efficiency.
Combustion efficiency looks at increased combustion temperatures which require the latest coating technologies to prevent heat damage to the components in the hot gas flow.
Mechanical efficiency looks at reducing losses in the power train, including the clearance between the rotor blades and the stator casing.
The clearance is crucial in determining the efficiency of the turbine and therefore a large part of its costs and productivity. Zirconia-ceramic materials can be used to minimize this clearance in high temperature applications. Clearance-control coatings or abradable coatings, function by allowing a rotating part, such as a blade, to cut a path in a sealing abradable layer with minimum clearance. Many advanced gas turbines use a thick ceramic coating to impart both thermal-barrier and abradability properties.
Future proofing
As design technology and materials’ science advance the newest generation of turbine components can present a considerable challenge to repair specialists. Finding the most suitable coating depends on a number of factors including adhesion qualities, heat and erosion resistance as well as compatibility with the design of the component.
For example, the challenges of protecting components, especially those within the hot section of a gas turbine, are considerable, especially when the temperature of the combustion gas is higher than the melting point of the base materials. The combination of internal cooling ducts and a thermal barrier coating (TBC) work together to maintain the desired component temperature. The latest turbine blades are designed with a large number of tiny cooling holes, often in excess of 500 in a single part, which must remain unaffected by the coating process.
Conventional thermal spraying processes would block off many of the holes, rendering the cooling system almost useless. However, new coating techniques are required to ensure that none of the cooling ducts are closed off by using conventional plasma spraying processes. Sulzer has addressed this and many other challenges in this area to deliver a bespoke service that ensures the latest techniques are adapted to suit each application.
It is essential that repair specialists, such as Sulzer, continue to develop new coatings and new application methods that can keep pace with the advances in the turbomachinery sector. In this way, plant operators will have the confidence to invest in repairs that have the ability to provide many years of continued service.
About Sulzer
Sulzer is the leading worldwide, independent service provider for the repair and maintenance of rotating machines including turbomachinery, pumps and electro-mechanical equipment. With a global network of over 150 technically advanced manufacturing and test facilities, Sulzer offers a collaborative advantage that delivers high-quality, cost-effective, customized and turnkey solutions, providing its customers with the peace of mind to focus on their core operations.
Sulzer Rotating Equipment Services, a division of Sulzer, can accommodate all brands of rotating equipment including turbines, compressors, generators, motors and pumps. With an enviable track record, dedicated teams of on-site engineers provide best-in-class solutions to ensure that the most effective service is delivered.
Sulzer is dedicated to providing superior service solutions to a range of industries including power generation, oil and gas, hydrocarbon and chemical processing, water and air separation. Every solution is customized to suit the business needs of each application – whenever or wherever that may be.
With a long history of providing engineering service support, Sulzer is headquartered in Winterthur, Switzerland where it began in 1834. Today, with sales over US$ 3B and with approximately 15,000 employees, the Sulzer footprint spans across the globe. The core aim is to deliver a flexible and cost-effective service that optimizes customer operational efficiency and minimizes downtime. For more information, visit www.sulzer.com.
Source: Sulzer